编码器精度
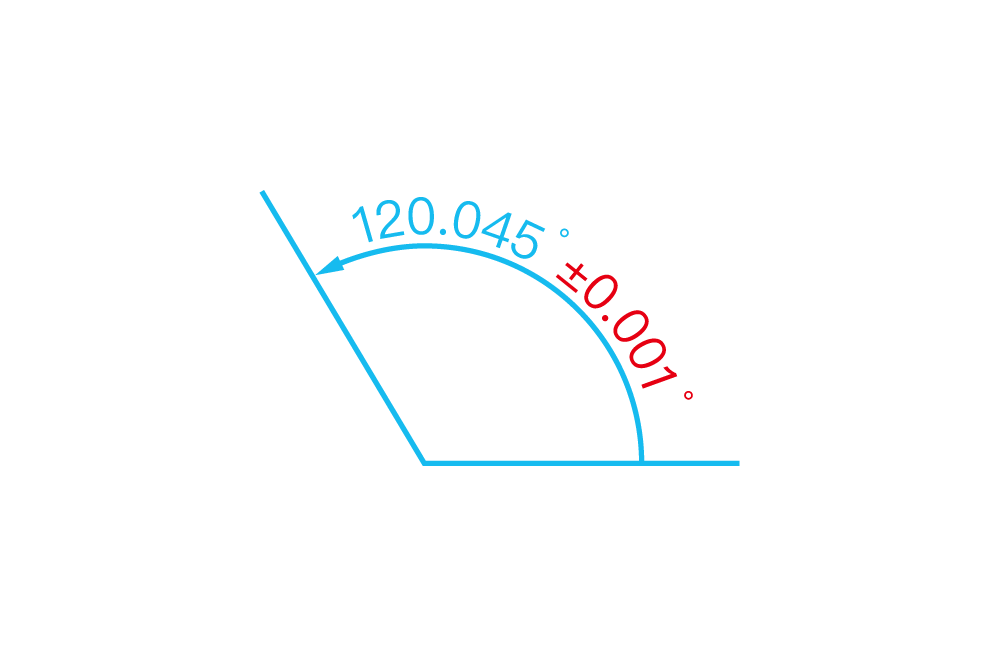
编码器用来测量角度,其基础也是一种测量设备,测量设备原理上就是将物理世界中的参数经过模拟测量后转化为数字信号,那就这个过程中一定会有测量误差以及影响误差的各种因素存在,本文就编码器精度进行介绍。
影响因素
首先,一个测量过程中,拥有至少两件物体:测量装置、被测量装置,影响最终测量结果的因素有:
- 位置:两个装置的相对物理位置
- 环境:该过程发生的周围环境
上两个因素是影响所有测量过程的主要基础因素,两者都会直接造成测量精度的偏差。
编码器精度
- 编码器作为角度测量装置,其拥有两种精度参数:
- 绝对定位精度
- 重复定位精度
绝对定位精度是指对于编码器测量得到的数据与真实物体世界的差值大小。(例:对于一个物体指向30˚方向,两个编码器同时测量到其指向的角度为30.08˚、29.98˚,那么第二个编码器则比第一个编码器精度在30˚位置时的精度更高。如果一个编码器在全量程也就是360˚中,每一个点位置的测量数据与真实物体角度误差在0.05˚内,我们则称0.05˚就是其绝对精度。)
重复定位精度是指编码器返回该位置时得到的数据与上次在该位置时数据的差值大小。(例:如对于一个物体指向30˚方向,编码器测量到的数据为30.02˚,然后物体运动到另一个位置后又返回30˚,编码器测量得到的数据为30.01˚,那么该过程中的精度为0.01˚。同理,编码器在全量程360˚中,每一个位置的返回值误差都在0.01˚内,那么这个0.01˚则是编码器的重复精度。)
可看出,绝对定位精度是基于状态的,其精度的参考坐标是真实物理世界;重复定位精度是基于过程的,其精度的参考坐标是上一次该位置的测量值。
位置因素
编码器中,每一种测量原理一定拥有测量装置(静件)与被测量装置(动件),将被测量装置与实际应用中要测量的物体联结,测量装置与要其壳体联结,则这时就引入了两个误差:
- 动件安装误差
- 静件安装误差
这两个误差再加上被测量物体运动时的抖动误差,都影响着动静件之间的相对位置,则影响测量得到数据的精度。
环境因素
由于各种测量原理的不同,每一种原理对环境的影响因素略有不同。
- 温度:各种原理都要面对的问题,均提出了相应的解决方案、算法。
- 固体颗粒(灰尘、杂物):光电编码器较敏感,会影响码盘上光的通过,造成丢数甚至数据错误。解决:完整的密封壳体封装
- 湿度:感容式编码器较敏感,会影响电容率,进一步影响获取到的数据。解决:密封隔绝
- 液体:光电编码器、感式编码器较敏感,会影响光电的光通过率,感容式的电容率。解决:密封壳体或封胶密封
- 磁干扰:磁编码器较敏感,会与磁环的磁场叠加。解决:金钢科技磁屏蔽罩方案
磁编码器
各种原理中,磁编码器抗环境干扰能力最强,可以直接在极其恶劣的环境中工作。
金钢科技的磁编码器专利,提供超高精度的安装方式,同时拥有极佳磁屏蔽保障的测量环境,为编码器的精度保驾护航。而且编码器均为一对一进行标定,解决了磁在加工过程中的不一致性带来的精度不一致问题,更高程度地保障了输出数据的可靠性。